Leiritz has invested in an AXIA-85 milling machine to enhance its production of large components.
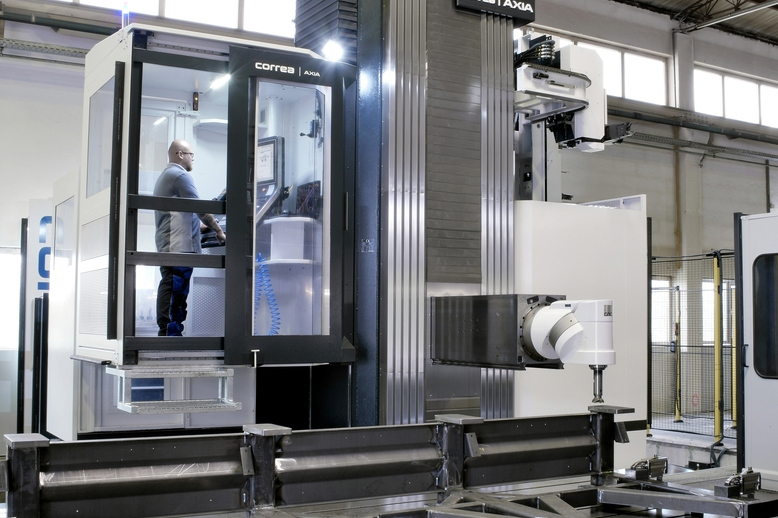
Leiritz Maschinenbau GmbH, a medium size company based in Bavaria (Germany), specialises in the complete manufacturing of innovative equipment and special machine construction solutions. “We currently have an even distribution of turnover between the two business areas: contract manufacturing and special machine construction”, says Alexander Ehard, managing partner of Leiritz together with his brother. "In the past we had problems with outsourcing machining of large parts, so we started to do it in-house" explains Sebastian Ehard, technical managing director and head of design.
Pendular machining
Nicolás Correa has already convinced the two company bosses when they bought a bed type machine NORMA in 2017; all special requests, such as pendular machining, a wider access surface to the machine bed, were fulfilled. "The pendular machining is very valuable for us; the second working surface allows us to reduce set up time" remarks the technical managing director.
When they needed to replace its old floor type milling machine, Leiritz decided to purchase an AXIA with travels of 8.5 m in the X direction, 3 m in the Z direction and 1.75 m in the Y direction. Welded assemblies with a weight of up to 20 tones and a length of up to 8.5 metres were to be processed on this machine with tolerances of three hundredths.
“We not only want to replace the old machine but also to expand our machining capabilities" says Alexander Ehard. His brother adds: "the aim was to improve the speed and implement machine data acquisition and analytics. We need to work in pendular in this machine too; in pendular mode, we could increase our usual spindle running times by 30 to 40%."
Machine fully adapted to customer’s requirements
Machine’s technical requirements were only half of the project, Leirtiz needed to keep the guarding of the old machine, the table and part of the foundation from the old machine, explains Sebastian Ehard. This AXIA was larger than the previous one and there was a shortage of space, however, everything fitted during the six-week installation and the machine was commissioned on schedule on 30 July last year.
Stability through box-in-box construction
A special feature of the AXIA is its box-in-box design with the ram, which is usually mounted on the side of the column, located in the centre of the box. "The centric guidance of the RAM in the box-in-box system achieves a symmetrical distribution of all forces thus higher stability and accuracy". "In addition, this way the thermal expansion is the same on all sides." For the Ehard brothers, this is another argument for choosing Correa.
After the first few months in operation, the conclusion is consistently positive. "The employees are thrilled with the AXIA in terms of accuracy, speed and operation," Alexander Ehard states. "Compared to the old machine, we are about 30% faster in terms of machining time".
Availability has also increased, and longer travels mean that one or two set-ups can be omitted. "In addition, the cooled milling head allows us to now mill components dry without the head threatening to overheat." Leiritz still sees potential in the machining of large parts and Sebastian Ehard reveals: "First of all, the construction of a new assembly and warehouse is planned. After that, there will be room for the next machine".
*Original article published on NC Fertigung